October 21, 2024
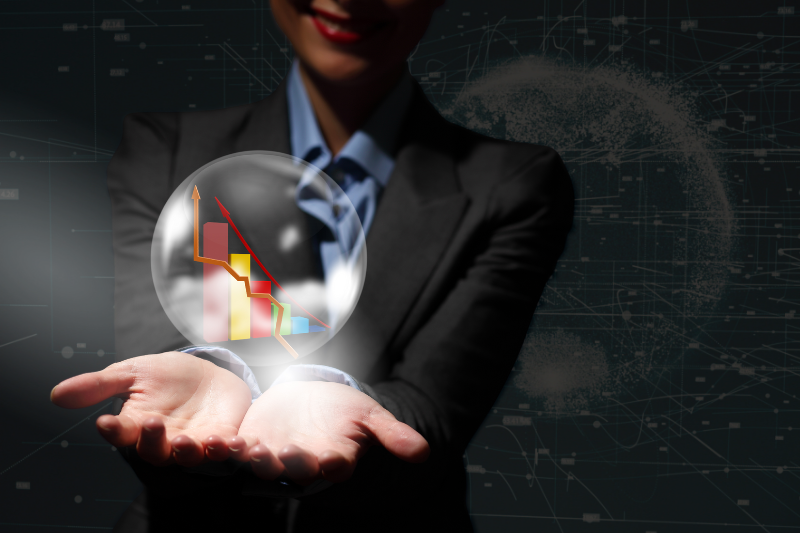
Process mining goes beyond process modeling, using advanced visualization and AI-powered analysis techniques to drive operational efficiency. By leveraging digital footprints found in a software system’s event log data, including unique process identifiers, user engagement events, event descriptions, timestamps, resources, costs, etc., process mining can identify bottlenecks, deviations, and other inefficiencies that are not transparent through normal observation.
Next-Level Process Intelligence
Process mining paints an accurate picture of what is happening within a process from beginning to end, using data to measure the time to complete each step, detect non-conforming variants, and identify opportunities to automate tasks. As an example, one manufacturing company used a process mining tool to analyze a supply chain process and found that after purchase orders had been released, the user was going in to change the price 14% of the time. Since this is not how the process was designed, an opportunity to apply corrective action was discovered. With each corrective action, the manufacturing company increases its return on investment (ROI) of its ERP system, positively impacting overall profitability.
Operational Insights Drive Continuous Improvements
Most businesses have some visibility to what is happening through dashboards and data science analytics that enable them to look at some trends. However, process mining provides the ultimate validation of what is happening, providing insights that were never before available. The right process mining solution transforms operational insights using advanced analytics to reveal hidden patterns and inefficiencies within organizational processes. These insights enable better decision-making to drive continuous improvements and sustainable growth.
Reduced Costs, Happier Customers and Employees
Like any new business technology, the real value is determined by its impact on employees and customers. “If users are struggling within a process and doing things that lead to errors and inefficiencies, there is a cost,” says Guide Technologies Vice President of Sales Consulting Ron Clontz. “For one, it prevents them from spending time on more value-added and strategic activities, such as developing customer relationships. Instead, they are stuck in a mundane transactional flow. Uncovering these inefficiencies and automating these tasks leads to time and cost reductions, improved customer satisfaction, and happier employees.”
Continuing to pursue a process that employees find difficult to complete without deviations causes disruptions throughout the organization. Process mining not only shines a spotlight on the problem but also reveals opportunities for automation that can eliminate employee frustrations and help reduce the need for cross-training. It enhances employees' jobs by removing things they do not enjoy, such as data entry.
Process Mining Success Stories
A manufacturing company that offered after-sale services discovered redundancies and delays in its billing processes through process mining. Taking corrective action, they were able to streamline the process and reduce redundancies by 40%. Without process mining, it would have been very difficult to understand what was happening due to the sheer volume of transactions that had to be analyzed.
A second company reported that their procurement process was plagued with serious delays and non-conformance issues. Talking to employees and actively observing their actions did not reveal the source of the problems. The company used process mining to capture data down to the task level, showing exactly where the delays occurred. They corrected the process to eliminate the issues and continued to monitor the process to ensure adherence to it, estimating a 25% improvement.
What’s Next?
Manufacturers are looking for insights that can help them drive business through automation. Competition is tough, margins are tight, the risk of non-compliance with regulatory demands is huge, and everyone needs to reduce costs. Process mining enables businesses to really begin to see the impact of process errors or deviations and to remove that last mile of inefficiency. It is the next step in the digital transformation journey.
“I think the next phase will probably focus on predictive capabilities,” said Clontz. “The ability to predict the likelihood of a recurrence happening in the future or anticipate bottlenecks before they occur will be like having a crystal ball.”
Infor’s Process Intelligence Suite
Infor Process Mining is the latest addition to the Infor Process Intelligence suite. The Process Intelligence Suite is a powerful analytics platform that enhances operational efficiency and facilitates data-driven decision-making across organizations. The suite enables users to quickly identify inefficiencies and bottlenecks by providing real-time insights into business processes, allowing for timely interventions. Advanced analytics, including machine learning and data visualization tools, empower users to uncover trends and derive actionable insights that inform strategic process decisions.
The suite integrates seamlessly with existing Infor CloudSuite applications and other enterprise systems, delivering a comprehensive view of organizational business process performance. With its user-friendly interface, individuals at all skill levels can effectively navigate and analyze data, fostering a culture of continuous improvement. Overall, Infor's Process Intelligence Suite positions organizations to thrive in a competitive landscape by streamlining workflows and driving sustained operational excellence.
Contact us today if you are ready to uncover actionable insights, optimize business processes, and gain efficiency across your business processes.