June 12, 2023
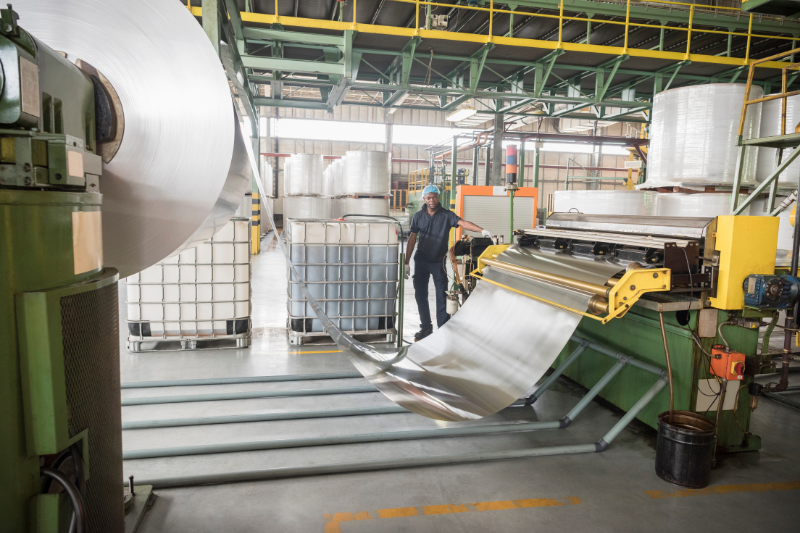
Roll forming is a highly utilized manufacturing process in various industries, including automotive, construction, aerospace, and appliance manufacturing. While it offers numerous advantages, there are common errors that can substantially impact the profitability of roll forming manufacturers. In this blog post, we will delve into these errors and explore practical strategies to avoid them. By implementing these ideas, roll forming manufacturers can minimize waste, optimize production, and enhance their financial performance.
Material Waste
Inefficient use of raw materials can lead to significant costs. If the roll forming process is not properly optimized or if the material is not loaded correctly, it can result in excess waste. This waste can include both scrapped parts and unused material, which can add up over time.
To reduce waste and maximize material utilization, manufacturers can employ the following strategies:
Accurate Material Planning: Thoroughly analyze customer requirements and optimize the material planning process. Precise measurements, minimizing tolerances, and utilizing nesting software can help maximize material utilization.
Optimized Loading: Train operators to load materials efficiently, ensuring proper alignment and avoiding unnecessary scrap. Consider investing in automated material handling systems to streamline this process.
Machine Downtime
Roll forming machines require regular maintenance to ensure they operate at peak efficiency. Neglecting maintenance or failing to address issues promptly can result in unplanned downtime. This downtime leads to lost production time and revenue. It's important to establish a preventive maintenance schedule and address any machine malfunctions promptly to minimize downtime.
To minimize downtime and maximize productivity, manufacturers should consider the following measures:
Preventive Maintenance: Establish a comprehensive maintenance program that adheres to manufacturer recommendations. Regularly inspect and maintain equipment, including lubrication, tooling checks, and calibration, to prevent breakdowns and minimize downtime.
Real-time Monitoring: Implement sensor technology to monitor machine performance and detect potential issues in real-time. This proactive approach allows for timely maintenance and minimizes unexpected downtime.
Tooling Errors
Roll forming relies on precise tooling to create the desired shapes and dimensions. Errors in tooling design or fabrication can result in defective or inaccurate parts. These parts may need to be scrapped or reworked, leading to additional costs and delays. Regular inspection and maintenance of tooling is crucial to avoid such errors.
Manufacturers can take the following steps to mitigate these errors:
Robust Tool Design and Fabrication: Engage experienced tooling engineers who understand the specific requirements of different industries. Implement rigorous quality control measures during tool fabrication and conduct regular inspections to identify and rectify any issues promptly.
Tooling Maintenance: Establish a tooling maintenance schedule to ensure tools are in optimal condition. Regularly inspect for wear and damage, and replace or repair components as necessary.
Quality Control Issues
Inadequate quality control can lead to costly problems. If defective parts are not identified and removed from the production line, they can result in customer complaints, returns, or even product recalls. Implementing robust quality control measures, including inspections at various stages of production, can help catch errors early and reduce costs associated with poor-quality products.
Consider the following measures for effective quality control:
Inspection at Every Stage: Implement a comprehensive quality control process that includes inspections at each stage of production. This includes raw material inspection, in-process inspections, and final product inspection.
Employee Training: Provide thorough training to employees on quality control procedures, emphasizing the importance of attention to detail and adherence to specifications.
Inefficient Workflow
A poorly optimized workflow can lead to inefficiencies and increased production costs. For example, if the sequencing of jobs is not planned properly, it can result in excessive setup times, longer changeovers between product runs, and decreased overall production output. Analyzing and improving the workflow, including optimizing production schedules and minimizing changeover times, can help reduce costs.
Manufacturers can implement the following strategies:
Production Planning: Utilize production planning software to optimize job sequencing, minimize changeover times, and maximize overall production output.
Lean Manufacturing Principles: Implement lean manufacturing principles to eliminate waste, streamline processes, and improve overall efficiency. This includes practices such as 5S organization, standardized work procedures, and continuous improvement initiatives.
Inaccurate Cost Estimation
Incorrectly estimating the cost of roll forming projects can lead to financial losses. Underestimating costs can result in selling products at a loss, while overestimating costs may make the prices less competitive. It's important to accurately assess the costs of materials, labor, machine usage, and other factors when quoting prices to customers.
Precise cost estimation is vital for profitability. Consider the following steps:
Detailed Cost Analysis: Conduct a thorough analysis of material costs, labor, overheads, and machine usage to ensure accurate cost estimation. Regularly review and update cost data to reflect changing market conditions.
Collaboration with Sales and Engineering: Foster close collaboration between sales, engineering, and production teams to ensure accurate cost estimation for each project. This collaboration facilitates a better understanding of customer requirements and helps avoid cost estimation errors.
Maximize Financial Performance
Roll forming manufacturers can significantly improve their profitability by addressing and mitigating common errors that impact costs. By implementing effective strategies such as optimizing material usage, minimizing machine downtime, ensuring tooling quality, maintaining rigorous quality control, optimizing workflow, and accurate cost estimation, manufacturers can avoid costly mistakes and maximize their financial performance. With a proactive approach, roll forming manufacturers can achieve efficiency, reduce waste, and enhance their competitive advantage in the market.
Whether you struggle with one or all of them, the right technology AND the right technology partner can help you avoid the aforementioned errors. Learn how Infor CloudSuite Industrial ERP can improve processes and data accuracy and Guide Technologies' manufacturing experts can tailor Infor manufacturing solutions to your unique needs.