July 31, 2023
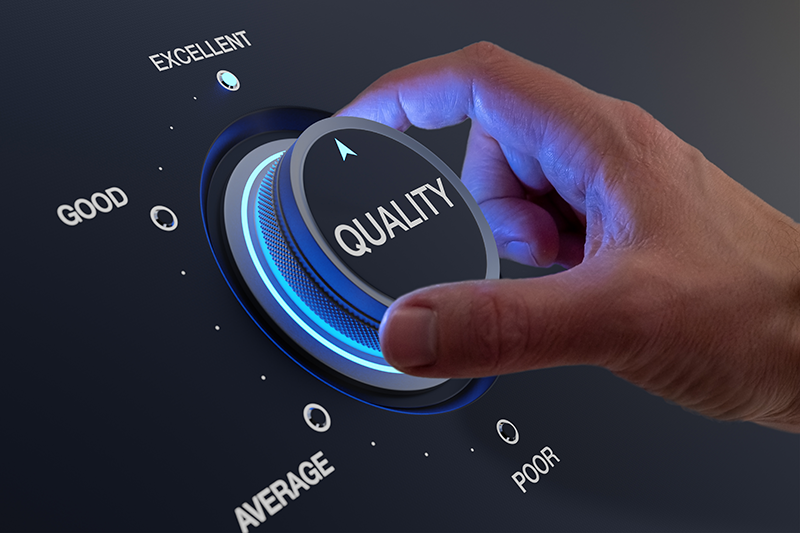
In today's fiercely competitive market, the importance of quality control and assurance (QC&A) in manufacturing cannot be overstated. These essential processes go beyond simply ensuring that products meet customer expectations; they are the bedrock of brand reputation and sustainable growth. By fostering a culture of excellence and uncompromising dedication to quality, QC&A instill confidence in consumers, enticing them to choose your products over competitors. But beyond the superficial benefits, QC&A prove their value by delivering tangible and cost-saving advantages.
Adhering to rigorous QC&A standards empowers manufacturers to steer clear of regulatory pitfalls, promoting seamless compliance and mitigating the risk of fines and legal entanglements. Moreover, QC&A contribute significantly to the safety of end-users, fostering trust and loyalty among customers who know that their well-being is a top priority. As these quality practices become entrenched, they pave the way for a dynamic and responsive approach to improvement, underpinning the journey of continuous growth that successful companies undertake.
QC & QA: Related but Distinct Concepts
Diving deeper into the essence of these intertwined concepts, it is vital to recognize that while quality control (QC) and quality assurance (QA) share the same destination, they follow distinct paths. QC is the vigilant gatekeeper, diligently identifying and rectifying defects or deviations in the final product. It places its focus on rigorous inspections and testing at various stages of production, assuring the desired level of quality is met before products reach the customers' hands.
QA, on the other hand, is the master architect, building quality into the very foundations of the manufacturing process. By designing and implementing robust systems and processes, QA prevents defects from arising in the first place, fostering a proactive approach to quality that transcends mere inspections.
Best Practices to Improve QC&A
Whether before, after, or during production, having solid quality control and quality assurance processes in place is a requirement for manufacturers who want to optimize productivity, operate efficiently, and perhaps most importantly, attract and maintain happy customers.
Here are some best practices to consider as you seek to improve QC&A:
Define & Establish Quality Standards & Quality Control Processes
To achieve the pinnacle of success in QC&A, manufacturers must adopt a holistic set of best practices. Foremost among them is the clear definition of quality standards, leaving no room for ambiguity regarding the desired level of excellence. By establishing well-defined quality criteria, tolerances, and specifications, manufacturers lay the groundwork for consistent, top-tier products. Essential to this process is the implementation of robust quality control processes, including inspections, testing, and sampling, which act as sentinels guarding the production line.
Monitor Production Processes & Train Employees
For continued success, vigilant monitoring of production processes is crucial, where the vigilant eye of manufacturers tracks key performance indicators (KPIs) such as defect rates, scrap rates, and yield rates. Equally vital is the nurturing of a workforce knowledgeable in QC&A processes, achieved through thorough training. When equipped with knowledge of quality standards, control processes, and tools, employees become ambassadors of excellence, aligning their actions with the company's commitment to delivering superior products.
Use Quality Control Tools & Implement Corrective Actions
Quality control tools, such as statistical process control (SPC), control charts, and Pareto charts, lend a data-driven edge to the pursuit of excellence. These invaluable instruments help manufacturers detect trends and patterns in quality data, empowering them to make informed decisions that strengthen product quality. When quality issues inevitably surface, the implementation of corrective actions becomes an imperative. Pinpointing the root cause of such issues and enacting lasting solutions ensures continuous improvement and instills resilience in the face of challenges.
Continuously Improve
In the relentless quest for quality, complacency has no place. Embracing a culture of continuous improvement is the key to unlocking new heights of success. Regular reviews of quality metrics, honest introspection, and a willingness to adapt to change are the cornerstones of progress. With each step forward, manufacturers inch closer to the realm of perfection, driven by the unwavering commitment to satisfy their customers' needs and exceed their expectations.
QC&A: The Defining Factor of Manufacturing excellence
The symbiotic relationship between quality control and assurance illuminates the path to manufacturing excellence. Embracing these principles not only secures a place in the hearts of discerning consumers but also fosters a reputation that withstands the test of time. As manufacturers embark on this transformative journey, they lay the foundation for sustainable growth and solidify their position as trailblazers in an ever-evolving industry. The marriage of QC&A becomes the defining factor in their success, breathing life into products that bear the mark of true distinction.